A niche, high-value added product and an ever-growing industry – technical textiles play an important role in almost every sphere of social and economic activities. An amalgamation of technology with textile materials offers a wide range of solutions to various industries. Technical textiles are thus, those textile materials that fulfil the primary criterion of providing functionality or suiting required performance characteristics. Some application markets specify the aesthetics of technical textiles as well and do not disregard it completely.
The advantages offered by technical textiles
- Lighter weight while being durable
- Renders the product multifunctional
- Production is flexible, continuous, and versatile
- Cost-effective and user friendly
- Environmentally sustainable
This article is the first of four articles in the series – Medical Textiles. Prior to understanding medical textiles, an overview of the technical textiles sector will provide insights into the basic idea, market scenario, and application areas.
1. Fibres used in technical textiles
The demand for multi-functional performance by technical textiles has led to the use of an array of raw materials. Fibres used in technical textiles could be natural fibres, regenerated fibres, synthetic fibres, mineral fibres, metal fibres, as well as certain speciality fibres.

Figure 1: Fibres for Technical Textiles
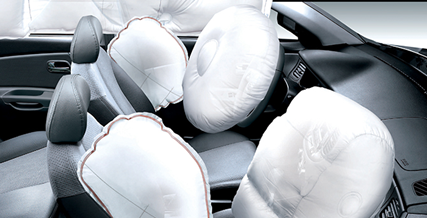
Figure 2: Woven fabric for an airbag | Image source: http://www.hyosungadvancedmaterials.com

Figure 3: Woven fabric for Medical Scrub Suit

Figure 4: Knitted fabric structure for (a) medical bandage and (b) glass fibre multiaxial fabric
Image sources: https://www.tigermedical.com/, https://tianmagroup.en.made-in-china.com/
The benefits that these fabrics carry are:
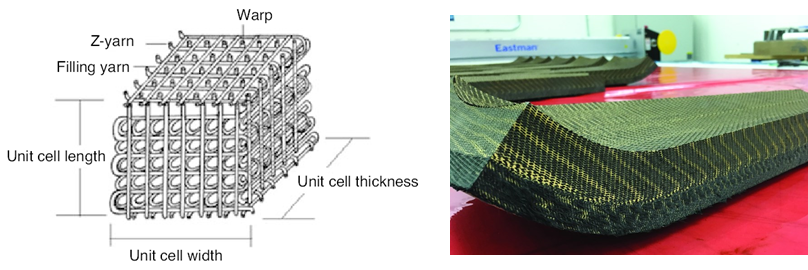
Figure 5: 3D woven fabric structure and application in the heatshield | Image source: Composites world
Figure 1: Fibres for Technical Textiles
2. Production processes of technical textiles
Weave and knit formation
Woven and knitted fabrics in technical textiles are very common for applications that require high strength and durability. Heavy technical fabric such as airbags, conveyors, sailcloth, bulletproof fabric, bolting fabric, artificial woven grass, cement bags, filtration fabric as well as the light technical fabric used in medical apparel, sportswear is woven fabrics. Both warp-knitted and weft-knitted structure fabrics find applications in technical textiles, commonly in sportswear. Multiaxial stitch-bonded fabrics are used in aircraft, automotive, ship and boat building, sports equipment, and rotor blades for wind power generation. Elastic and non-elastic bandages, abdominal bandages are also made of a knitted structure.Figure 2: Woven fabric for an airbag | Image source: http://www.hyosungadvancedmaterials.com
Figure 3: Woven fabric for Medical Scrub Suit
Figure 4: Knitted fabric structure for (a) medical bandage and (b) glass fibre multiaxial fabric
Image sources: https://www.tigermedical.com/, https://tianmagroup.en.made-in-china.com/
The benefits that these fabrics carry are:
- Cost-effectiveness
- Environmentally friendly
- High specific strength
- High stiffness (woven)
3D woven fabrics
3D woven fabrics serve as tough, lightweight alternatives to metals and allow for numerous customization options. 3D woven fabrics provide extra strength and stiffness, thus making it suitable for use in the transportation, heavy industrial, ballistics, aerospace, and marine sectors.Figure 5: 3D woven fabric structure and application in the heatshield | Image source: Composites world
Nonwoven formation
Nonwoven fabrics are a versatile material finding application in a wide range of industrial, health, and consumer products that extend from single-use disposable items such as teabags and wet wipes to highly durable products such as synthetic leather, automotive components, and roofing membranes. One of the main advantages that nonwoven production process holds is that labour costs in manufacturing are low compared to traditional textile processing as there is a high degree of process automation.The other advantages of nonwoven fabric for technical textiles are:
- Greater strength per basis weight than competing fabrics
- High levels of uniformity
- Form holding in the Z direction
- High tear and tensile strength
- Dimensional stability
- Consistency in high-temperature applications
- Application-specific engineering
- Ability to form composites for advanced performance
The different web structures
The different web structures formed as per the laying process are carded, air-laid, wet-laid, spun-bond, fibrillated films, melt-blown, flash-spun, and electro-spun webs. Chemical bonding (saturation bonding, print bonding, spray bonding), thermal bonding, solvent bonding, needle punching, stitch bonding, and hydro-entanglement bond the web. The application areas of these nonwoven fabrics are:- Carding and crosslapping – filtration media, floorcoverings, automotive interiors and headliners, shoe linings, geosynthetics, washable continence management pads, and wound dressings
- Airlaid and wetlaid – absorbent single-use hygiene products such as wipes, and other absorbent hygiene products
- Spunbond – filtration, erosion control fabric, medical wipes, incontinence products
- Meltblown – filter media and lightweight single-use hygiene products, facemask filter, air filter, heavier weight fabrics (>100gm–2) as oil sorbents
- Flashspun – printing or writing substrates, protective clothing in the chemical, electronics, health care, nuclear and oil industries
- Electrospun – sound absorption, filtration applications
- Fibrillated films – filtration and packaging and as layers in composite nonwovens
- Similarly, the end-use application depends on the bonding process as well, like:
- Saturation bonding – interlining fabric for textile clothing
- Print bonding – single-use protective clothing, cover stock and wipes, domestic dishcloths and dusters
- Spray bonding – filling in quilted fabrics, for duvets and for some upholstery; for abrasive pads for polishing and cleaning operations
- Thermal bonding – substrate for tufted carpet, coating substrates, hygiene coverstock, interlinings
- Needle punching – filtration, geosynthetics, papermakers’ felts, synthetic leather, floorcoverings, automotive headliners, and wound dressings
- Stitchbonding – ticking for mattresses and beds, fabrics used in training shoes, terry towelling, tufted carpets
- Hydroentanglement – dry and pre-moistened wipes, medical gauze, surgical gowns, scrub suits, sheets and drapes, protective clothing liners and moisture barriers, automotive components and filtration
Figure 6: Nonwoven Air-Filtration Media
Figure 7: Nonwoven fabric for a facemask, headcover, and apron
Braiding
Braiding is a simple form of narrow fabric construction. It is done by an intertwining of yarns in whatever direction suited the maker's purpose. Braiding can be two-dimensional or three-dimensional. These fabrics function as tension textiles. The braided yarns are used as cordage, webbings, strappings, belts, tapes, nets. This structure also finds a use for medical applications such as sutures, stents, ligaments, tendons, floss, and scaffold.Figure 8: Braided yarns
3. Finishing and Coating in technical textile production
Mechanical or chemical finishes textiles enhance the appearance, aesthetics, properties, and performance to meet the functional requirement. Finishes that may be given to technical textiles and the functionality that is rendered is shown in the table below.Technical textile fabrics are coated to confer additional properties to the material. A range of chemicals is applied on the substrate, such as polyvinyl chloride, polyethylene or polypropylene, polyurethane, acrylics, rubber, waxes, and hot melt epoxy resins. The coating chemical may be applied on either surface to be coated or is impregnated into the structure of the fabric.
Why technical textile is a sunrise sector
Tapping on the unique properties and advantages that technical textiles provide, a lot of developmental work is involved in making the material more advanced, in terms of performance and functionality requirements. Innovation is constant in this industry, and there are a number of growth enablers, making it a sunrise sector. Over the past ten years, Asia is emerging as a powerhouse both for production and consumption of technical textiles with China being a market leader. Korea, Japan, India and Taiwan are the other key players of technical textiles in the Asian continent. As per Allied Market Research, the global technical textile market was valued at $201.2 billion in 2019 and is projected to reach $274.1 billion by 2027, growing at a CAGR of 5.1% from 2020 to 2027. The Technical Textiles sector in India is estimated to be growing at a rate of 12% per annum, and the government aims to increase this to 20%.
The factors driving the growth of technical textiles are
- Industrialization and increased need for technical textiles in markets like agriculture, automotive, healthcare, infrastructure, oil & petroleum, etc.
- Increased demand for hygiene and medical products by consumers
- Growing environmental awareness driving the need for more filtration, oil absorbent, landfill backing products
- Government initiatives like FDI promotion enabling leading global manufacturers of technical textiles products will thus be able to establish manufacturing units in India
- Higher returns compared to conventional textiles attracts entrepreneurs.
Application Areas of technical textiles
Technical textiles have diverse application areas. Some of them being aerospace, construction, furniture, food, medical, automotive, defence, sports, apparel, civil engineering, mining, electrical, agriculture, etc. Based on the application areas, technical textiles are categorized as shown in the figure below:Figure 9: Classification of Technical Textiles
Classification of technical textiles and a brief explanation of these textile categories
- Agrotech – Textile products for agriculture, forestry, horticulture, and landscape gardening. Examples: crop covers, seed blankets, greenhouse shading, rootbags, fishing nets
- Buildtech – Textile products for membrane construction, lightweight and solid structures, earthworks, hydraulic engineering, and road construction. Examples: roofing and tile underlay, thermal and noise insulation, pipe wrap, reinforcements
- Clothtech – Innovations in shoe and clothing manufacture. Examples: cleanroom garments, interlining, leather goods applications
- Geotech – Products in road construction, civil engineering, and dam and waste site construction. Examples: erosion prevention, asphalt overlay, drainage, offshore land reclamation
- Hometech – Innovations in the manufacture of furniture, upholstery, floor coverings, and carpets. Examples: carpet backing, air and water filtration, drapes
- Indutech – Products for mechanical engineering and for chemical and electrical industries. Examples: electrical components, filtration media, conveyor belts, noise absorbents, cordages
- Medtech – Innovations in medical and hygiene products. Examples: drapes and gowns, sterile wrap, wound care, protective apparel, bedding, masks
- Mobiltech – Textiles for ship and aerospace construction as well as automotive, railway, and space travel. Examples: heat shields, engine intake and exhaust filters, silencer pads, car covers, car mats, seat covers, airbags
- Oeko-tech – Products for environmental protection, waste disposal, and recycling. Examples: wastewater filtration, dust collection, oil absorbent, gas and odour removal
- Packtech – Innovations in packaging, covering, and transportation. Examples: bulk packaging, packaging spacer, teabags
- Protech – Innovations in personal and property protection. Examples: chemical and biological protection, flame retardant clothing, cut resistant clothing, hazardous waste control
- Sportech – Innovations in the sport and leisure world. Examples: sport equipment, sportswear, camping equipment
Figure 10: Technical Textiles Application Areas
References
A. R. Horrocks and S. C. Anand, Eds., Handbook of Technical Textiles, 2nd ed., vol. I, Woodhead Publishing, 2016.T. Matsuo, “Fibre materials for advanced technical textiles,” Textile Progress, vol. 40, no. 2, 2008.
https://www.technicaltextile.net/. [Accessed September 2020].
https://niti.gov.in/technical-textiles-sun-rising-sector-indian-textile-industry. [Accessed September 2020].