Caps have always been one of the most common fashion accessories we all can agree to have in our closet. With numerous variations in caps both for men and women, the baseball caps or snapback caps have been the most iconic cap of all time which can be worn by both men and women alike. This article will focus on the process of manufacturing the iconic baseball cap.
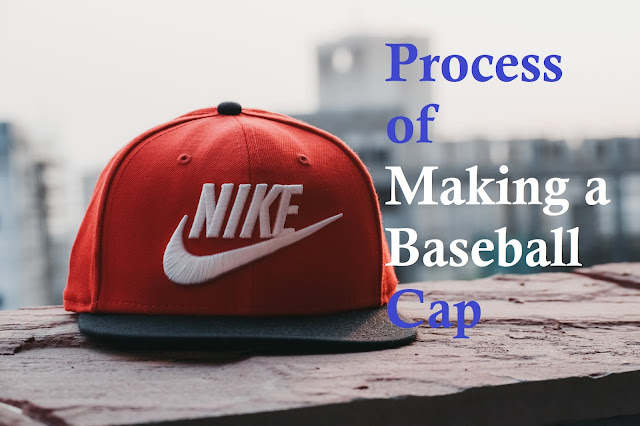
Related Article: 17 Different types of caps (with pictures)
2. The stitching process of the crown and visor can start simultaneously as they are made separately and attached before the final process. The stitching starts with the front panels first through SNLS machine. Often due to cap design, another layer of fusing fabric is added to the back of the front panel. This gives the raised shape to the crown.
3. Embroidery on the panels: After this, the front panel is sent to the embroidery department where distinct logos and graphics are embroidered onto the front panels through computerized embroidery machines.
4. Attach eyelets on the panels: After embroidery, the panels are sent to eyelet machines where the machine pierces through the panel and stitch around its edges. Not all the panels are pierced but at least two needs to be there so that proper air circulation happen which could vent out the heat building under the cap.
5. Attach tapes: With most of the caps being 6 panelled caps the stitching starts with stitching 3 panels together twice which is stitched in between and reversed to form the crown. After all the panels are stitched together fabric tapes are added onto the seams from the inside so that there are no exposed seam edges inside the cap. These tapes ensure that the seams give a soft feel to the wearer at the seams.
6. Make the visor part: Alongside the crown, the front visor is made by stitching two fabric panes like a pocket and turning it inside out. For a stiff visor often cardboard is inserted in between the fabrics and sealed from the hem. The material to be put inside the visor can range from stiff fabric to plastic sheet depending on the requirement. After this 7-8 parallel stitch is stitched on the visor parallel to the visor hem which ensures that the bottom fabric doesn’t lose its shape with time. This is mostly done through automatic stitching machines for the highest quality.
7. After that, the visor is then attached to the crown and stitched.
8. Attach sweatband: With the visor attached, the sweatband is attached to the base of the crown followed by a decorative topstitch at the base of the cap. During this labels can be added to the sweatband.
9. Attach cloth snaps (button): The final stage is the addition of the cloth snaps at the top of the cap where all the panel seams converge.
10. Attach Closure: At the back of the cap attach an adjustable closure. This can be made of self fabric or plastic closure.
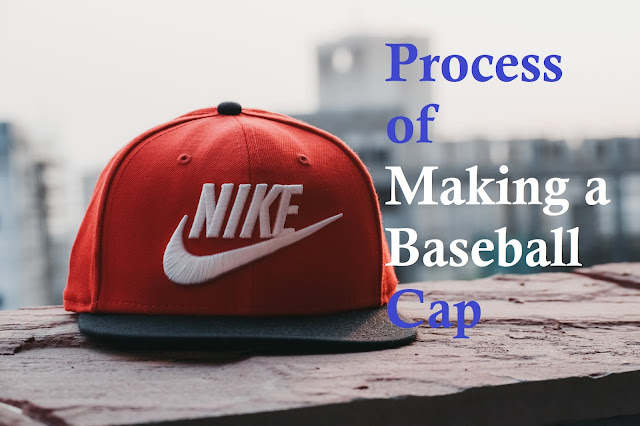
Components of a baseball cap
The process of making the caps starts with knowing about the components of the cap. Every baseball/snapbacks comprise of the following components:- Crown: The dome part of the cap is called the crown of the cap and is made by sewing mostly 6 triangular fabric panels together.
- Visor: This is the fabric sandwiched plastic/cardboard attached to the front of the cap which helps to shield the eyes from the sun. It comes in different shape and can steer the entire look of the cap.
- Top button: A fabric-covered metal button attached at the top of the cap which holds all the panels together.
- Closure: The back piece in the cap that allows for fit and adjustment. There are different types of closure ranging from snapbacks, plastic hooks and buckles.
Related Article: 17 Different types of caps (with pictures)
Baseball cap manufacturing process
1. The first stage of manufacturing starts with the cutting of fabric. All the cap components are of the same shape and size for most of the caps and thus hydraulic machines are mostly used to cut the panels. This is a fast, uniform and reliable way of cutting the panes and visors.2. The stitching process of the crown and visor can start simultaneously as they are made separately and attached before the final process. The stitching starts with the front panels first through SNLS machine. Often due to cap design, another layer of fusing fabric is added to the back of the front panel. This gives the raised shape to the crown.
3. Embroidery on the panels: After this, the front panel is sent to the embroidery department where distinct logos and graphics are embroidered onto the front panels through computerized embroidery machines.
4. Attach eyelets on the panels: After embroidery, the panels are sent to eyelet machines where the machine pierces through the panel and stitch around its edges. Not all the panels are pierced but at least two needs to be there so that proper air circulation happen which could vent out the heat building under the cap.
5. Attach tapes: With most of the caps being 6 panelled caps the stitching starts with stitching 3 panels together twice which is stitched in between and reversed to form the crown. After all the panels are stitched together fabric tapes are added onto the seams from the inside so that there are no exposed seam edges inside the cap. These tapes ensure that the seams give a soft feel to the wearer at the seams.
6. Make the visor part: Alongside the crown, the front visor is made by stitching two fabric panes like a pocket and turning it inside out. For a stiff visor often cardboard is inserted in between the fabrics and sealed from the hem. The material to be put inside the visor can range from stiff fabric to plastic sheet depending on the requirement. After this 7-8 parallel stitch is stitched on the visor parallel to the visor hem which ensures that the bottom fabric doesn’t lose its shape with time. This is mostly done through automatic stitching machines for the highest quality.
7. After that, the visor is then attached to the crown and stitched.
8. Attach sweatband: With the visor attached, the sweatband is attached to the base of the crown followed by a decorative topstitch at the base of the cap. During this labels can be added to the sweatband.
9. Attach cloth snaps (button): The final stage is the addition of the cloth snaps at the top of the cap where all the panel seams converge.
10. Attach Closure: At the back of the cap attach an adjustable closure. This can be made of self fabric or plastic closure.
11. Steaming the stitched cap: After stitching is complete, the caps are placed on a blocking machine that steams and fixes the shape of the cap. This ensures a greater life span of the caps as they are less likely to lose their shape after that.
For most of the operations, stitching can be completed with simple SNLS machines but for the visor and sweatband attachment a raised bed SNLS machine will be required as the full round of the crown hem needs to be stitched. Also, for attachment of the tapes, DNLS has to be used with a tape feeding folder.
For most of the operations, stitching can be completed with simple SNLS machines but for the visor and sweatband attachment a raised bed SNLS machine will be required as the full round of the crown hem needs to be stitched. Also, for attachment of the tapes, DNLS has to be used with a tape feeding folder.
References: https://flexfit-headwear.com/guide-parts-baseball-cap/
Image credit: https://www.pexels.com/@amanjakhar
Tags
Caps