This article is written by Adita Banerjee. She has written this post based on her learning in an internship assignment with a textile mill.
Formula – Pick-up% =

The purpose of this article is to identify the underlying cause of this variation and to provide a relevant solution to reduce it as much as possible.
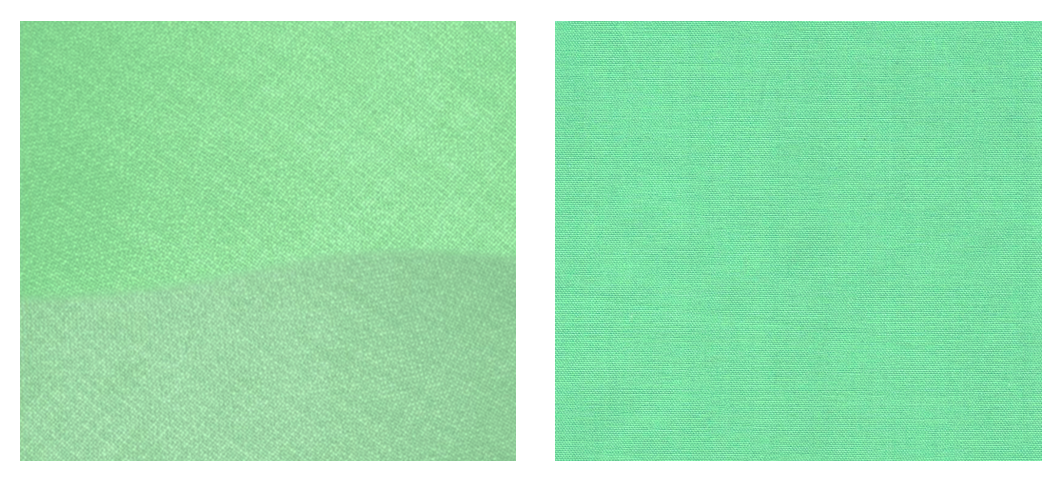
I have shared images of two fabric swatches. Which one would you prefer?
Obviously, the answer would be the right one. It is because there is no shade variation. Now this is a critical problem in the fabric processing department. This unit is in charge of processing the grey fabric in accordance with the buyer's specifications.
Among all the processes, dyeing is an important step in achieving the desired fabric colour. There will be a lot of shade variation if the dyeing is uneven. CSV is the most common of these variations. CSV is a centre-to-selvedge variation (shade) caused by uneven dyeing. It is a critical issue in the open width fabric processing industry, where continuous and semi-continuous dyeing machines are used. These machines offer low dye and chemical waste, high output, and low time consumption.
However, achieving the perfect shade is not always possible due to a variety of factors, resulting in shade variation from centre to selvedge. As a result, an increased number of fabrics are reprocessed each month to address this issue. The processing cost of fabric per metre rises as a result of this.
Ready for Dyeing (RFD) parameters.
(a) Absorbency
- Drop test to measure the time taken for a drop of water to get absorbed
- Fabric absorbency should be less than 3 second by water drop.
I have shared images of two fabric swatches. Which one would you prefer?
Obviously, the answer would be the right one. It is because there is no shade variation. Now this is a critical problem in the fabric processing department. This unit is in charge of processing the grey fabric in accordance with the buyer's specifications.
Among all the processes, dyeing is an important step in achieving the desired fabric colour. There will be a lot of shade variation if the dyeing is uneven. CSV is the most common of these variations. CSV is a centre-to-selvedge variation (shade) caused by uneven dyeing. It is a critical issue in the open width fabric processing industry, where continuous and semi-continuous dyeing machines are used. These machines offer low dye and chemical waste, high output, and low time consumption.
However, achieving the perfect shade is not always possible due to a variety of factors, resulting in shade variation from centre to selvedge. As a result, an increased number of fabrics are reprocessed each month to address this issue. The processing cost of fabric per metre rises as a result of this.
1. Checkpoints for CSV in a semi-continuous machines
Before dyeing a fabric lot, the fabric is prepared for improving dyeing. These fabrics are called RFD fabrics.Ready for Dyeing (RFD) parameters.
(a) Absorbency
- Drop test to measure the time taken for a drop of water to get absorbed
- Fabric absorbency should be less than 3 second by water drop.
(b) Fabric pH
- Few drops of pH solution is poured onto the fabric surface and the outline is observed
- Fabric pH should not drop below 5.5
- Few drops of pH solution is poured onto the fabric surface and the outline is observed
- Fabric pH should not drop below 5.5
(c) Whiteness index
- After calibration the fabric sample is tested with UV filter on in the spectrophotometer.
- Three readings are taken to check the whiteness value of the sample.
- Whiteness value for RFD fabric should not be less than 55%
(d) Peroxide content
- Fabric sample is wetted and pressed by peroxide strip for at least 20 secs.
- The colour of the strip after removal is observed.
- Fabric should be free from residual peroxide or alkali.
(e) Starch content
- Tegwa test is carried for Linen/Cotton blends as they are desized in singeing machine.
- Presence of starch shows improper desizing of fabric sample.
Machine parameters
- Adjusting nip pressure of squeeze rolls.
- Checking pick-up% of fabric sample just after dyeing.
- After calibration the fabric sample is tested with UV filter on in the spectrophotometer.
- Three readings are taken to check the whiteness value of the sample.
- Whiteness value for RFD fabric should not be less than 55%
(d) Peroxide content
- Fabric sample is wetted and pressed by peroxide strip for at least 20 secs.
- The colour of the strip after removal is observed.
- Fabric should be free from residual peroxide or alkali.
(e) Starch content
- Tegwa test is carried for Linen/Cotton blends as they are desized in singeing machine.
- Presence of starch shows improper desizing of fabric sample.
Machine parameters
- Adjusting nip pressure of squeeze rolls.
- Checking pick-up% of fabric sample just after dyeing.
2. Steps to checking dye pick-up%
- Take plastic pouches and weigh them on weighing machine and mention on the label.
- Take cut out of fabric from right, middle and left from the end and put them inside the plastics as mentioned.
- Then again weigh them on the machine to get the weight of the wet sample.
- After that take out and dry the fabric for 5-6 mins.
- Then weigh them to get the dry weight.
- Put it into the pick-up formula and there we get the pick-up%.
3. Procedure of checking CSV of dyed fabric:
To check the shade variation, cut a strip of fabric width wise from right, middle and left of the fabric roll.Figure- 1: Shade variation checking
Significance of Delta L*a*b* colour difference:
DL* = difference in lightness/darkness value (+ = lighter - = darker)
Da* = difference on red/green axis (+ = redder - = greener)
Db* = difference on yellow/blue axis (+ = yellower - = bluer)
DC* = difference in chroma (+ = brighter - = duller)
DH* = difference in hue
DE* = total colour difference value
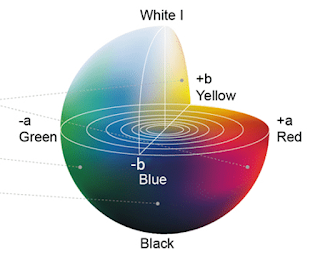
Figure-2: Colour difference in CieLAB (source: www.viewsonic.com)
- Now take one strip and cut it into 7 equal parts and number it as 1, 2, 3, 4 etc. sequentially
- Further stitch the pieces as shown in Fig-1.
- Now check for the shade variation under D65 light source.
- If there are no variations, fabric is acceptable but if there is a variation then fabric is reprocessed.
4. How to check CSV?
It is checked under D65 light source and confirmation is done with the help of spectrophotometer. The colour difference is checked in the Delta Cielab. Three core definitions provided by the CIE are the standard observer, the Lab colour space, and Delta E measurements.Significance of Delta L*a*b* colour difference:
DL* = difference in lightness/darkness value (+ = lighter - = darker)
Da* = difference on red/green axis (+ = redder - = greener)
Db* = difference on yellow/blue axis (+ = yellower - = bluer)
DC* = difference in chroma (+ = brighter - = duller)
DH* = difference in hue
DE* = total colour difference value
Figure-2: Colour difference in CieLAB (source: www.viewsonic.com)
5. Important points for CSV control
- CSV is one of the major defects among others like lab to bulk variation, tailing issue, etc.
- The fabric should contain no residual alkali, starch, or any other substance that would interfere with fabric absorbency.
- Uneven drying or moisture content affects the dye uptake of the fabric.
- Fabric should be spread properly to avoid folds, which can retain moisture. This will result in uneven dyeing.
- During washing of dyed fabric if the rolls give uneven pressure, then it has a chance of causing CSV.
- If the acid dosing is not even in both the sides, then it causes CSV.
- The fabric should be rolled properly and covered with polyethylene sheet. If the sheet remains open from one side, then there is a chance of CSV.
- If the temperature of the trough is not even throughout its width or the spray pipe is clogged it causes CSV.
Related article: List of garment defects (with images)
About the Author:
Adita Banerjee is pursuing her graduate degree in Textile Technology from the Government College of Engineering and Textile Technology, Serampore. She loves writing content and reading books.