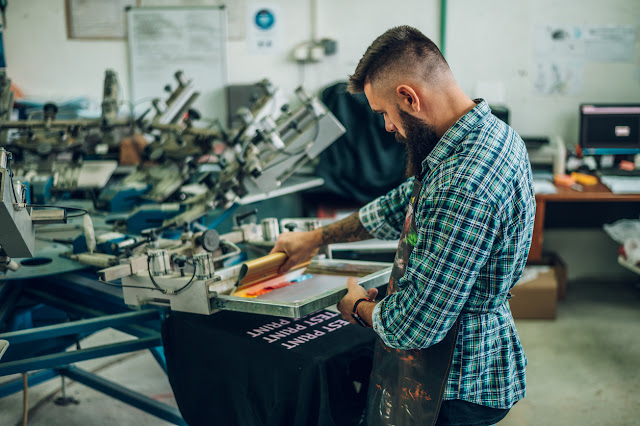
In a Tukatalks video, Mr. Ram Sareen argued that t-shirt screen printing should be done on fully stitched blank garments.
After reading this, I raised a few concerns about this new method of printing in the context of mass manufacturing of t-shirts for export orders.
Considering this an interesting idea, I thought of sharing this new idea with garment manufacturers who used to do screen print t-shirts on cut panels. (Let’s limit our discussion on screen printing on t-shirts and similar apparel products).
In the same video, he has shown how most of the American garment manufacturers do screen printing on the blank t-shirts. In contrast, in the Asian region garment manufacturers do not follow such a method when it comes for printing a design on the t-shirts for full-package export orders.
In this post, I will walk you through how much this new method is practical in terms of acceptance and application. Then I will discuss a few pros and cons of the new method of t-shirt screen printing.

I worked in a garment export house and managed many t-shirt orders from European buyers. We used to print designs on that cut panels or cut blocks for all t-shirt orders. The process flow was – cut the fabric and stick layer numbering sticker to each cut part (to identify lot, size, and ply number of the cut parts). Then send the panels to a printing unit.
After printing and curing process, printing house send back all the printed panels to the sewing factory. After receiving printed panels, cutting department matches the garment plies with other t-shirt components and prepare bundle for next process. Then bundles are sent to stitching floor. This works well with some inherent issues with the process.
In terms of printing equipment and workstations, print workshops use flat-bed table (tilted tabletop) and rotating octopus screen printing machine. For fled-bed screen printing, the design screen is manually aligned for the print placement and placed on the cut panels and then squeeze the color paste over the screen by two hands. In case of octopus printing machine, there are manual and automatic printing options. The cut panels are positioned on the printing plate manually.
Most common print positions in a t-shirt are front panel (any kind of artwork or graphics design), front chest (logo), back panel, back yoke inside just below the neckline and moon patch.
Get the printing done on ready garments (tees). For this, direct-to-garment (DTG) printers (a digital printing method), and octopus screen printing machines are used. This process is not new. But this new method is not often used in mass t-shirt production for printing designs.
In conventional screen printing of a t-shirt is done on cut panels (before the stitching process). Unfortunately, this practice causes a lot of issues with puckering later on, due to the shrinkage of the panel while the ink is cured with heat. Mr. Ram Sareen argues that screen printing should only be done on fully sewn blank garments, so that when they are heat set, the curing process shrinks the entire garment uniformly.
After reading this, I raised a few concerns about this new method of printing in the context of mass manufacturing of t-shirts for export orders.
Printing on fully sewn t-shirts is possible and benefits manufacturers in couple of ways as Mr. Sareen has explained in the video. You might be aware that all the print-on-demand/custom prints (t-shirts) are done on blank t-shirts for faster delivery.
I agree with shrinkage on panels due to curing process and puckering in seams.
But printing on ready t-shirts may not be applicable for all types of print designs and print placement on a t-shirt.
Another concerns - print defects found on panels can be easily replaced by cutting additional panels. But if printing defects found of ready t-shirts after printing, it would way more work to change the defective part (print related) or separate the whole t-shirt from the lot.
Considering this an interesting idea, I thought of sharing this new idea with garment manufacturers who used to do screen print t-shirts on cut panels. (Let’s limit our discussion on screen printing on t-shirts and similar apparel products).
In the same video, he has shown how most of the American garment manufacturers do screen printing on the blank t-shirts. In contrast, in the Asian region garment manufacturers do not follow such a method when it comes for printing a design on the t-shirts for full-package export orders.
In this post, I will walk you through how much this new method is practical in terms of acceptance and application. Then I will discuss a few pros and cons of the new method of t-shirt screen printing.
How does the conventional method of t-shirt screen printing work?

Image: Printing on cut panels | Image source: unsplash.com
After printing and curing process, printing house send back all the printed panels to the sewing factory. After receiving printed panels, cutting department matches the garment plies with other t-shirt components and prepare bundle for next process. Then bundles are sent to stitching floor. This works well with some inherent issues with the process.
In terms of printing equipment and workstations, print workshops use flat-bed table (tilted tabletop) and rotating octopus screen printing machine. For fled-bed screen printing, the design screen is manually aligned for the print placement and placed on the cut panels and then squeeze the color paste over the screen by two hands. In case of octopus printing machine, there are manual and automatic printing options. The cut panels are positioned on the printing plate manually.
Most common print positions in a t-shirt are front panel (any kind of artwork or graphics design), front chest (logo), back panel, back yoke inside just below the neckline and moon patch.
What is the new method of t-shirt printing about which we are talking?
The other method of printing t-shirts - cut the fabric, sew t-shirts, and then print the design on the ready t-shirts. If you do not have printing workshop inhouse, send the blank t-shirts to a printing subcontractor (the same way you used to follow currently).Get the printing done on ready garments (tees). For this, direct-to-garment (DTG) printers (a digital printing method), and octopus screen printing machines are used. This process is not new. But this new method is not often used in mass t-shirt production for printing designs.
Custom T-shirt printing services
In the on-demand print services, t-shirt printing is done on fully sewn t-shirts. They do printing on ready t-shirts by using different printing technology. They use thermal heat transfer printing or digital printing methods, instead of screen printing.Another difference is that print-on-demand services are normally used to execute single-piece orders or a few t-shirts at a time. The printing cost is higher than the mass screen printing cost.
In wholesale screen printing, bulk orders are common, often ranging from dozens to hundreds or even thousands of shirts. This method involves creating screens for each color in the design and then applying ink through those screens onto blank shirts. While screen printing companies offer lower per-unit costs for large orders, they require minimum order quantities, making them more suitable for high-volume orders.
Challenges in mass garment printing on ready garment form
1. Need to upgrade the printing set-up:As mentioned above, traditional printing units use flat beds for laying the fabric panels for screen printing. The same table can’t be used if they need to print on a ready t-shirt. Nowadays, garment printers have octopus rotatable printing machines.
For printing a design on a blank t-shirt, the printing unit need to upgrade their printing set-up (if not yet upgraded). They can’t use the same flat table for printing ready t-shirts.
2. Need to improve printing quality:
Mishandling of ready garment can damage the good t-shirts. Managing a cut panel and handling fill garment is completely different. So, skill training is required for workers in handling ready garments.
3. Handling of higher inventory/material:
With fully sewn garments, the volume will be higher in compared to single panel of a garment. So, transportation and handling cost will be higher as well. Even printing unit need to create more space for storing the incoming t-shirt for printing order.
The value of the fully sewn garment is much more than the cut panels. Therefore, sending ready t-shirts to an outside printing unit may be considered a risky process for order execution.
4. In-house printing machine and printing set-up would be useful.
For this initiative, one need consider investment for setting up a printing plant and machineries. This can be a separate cost center under the same roof. For long term, this investment would be beneficial for the company. Also, one need to understand that different types of garment printing needs cannot be managed by one unit.
When someone does export order for t-shirts and other items, order volume changes during the year, and each style may not need the same number of printed designs. So, utilization of the printing machinery and human resources. In such cases, the printing house can provide garment printing services to other garment manufacturers.
When someone does export order for t-shirts and other items, order volume changes during the year, and each style may not need the same number of printed designs. So, utilization of the printing machinery and human resources. In such cases, the printing house can provide garment printing services to other garment manufacturers.
Benefits of adopting the new process of printing T-shirts
1. Elimination of sorting and re-bundling process:When you sew the garments first and do printing on ready garment, you don’t need to do re-bundling and matching of panels prior to stitching. If you can eliminate a process from the t-shirt manufacturing, which would help you saving process time and money.
Ram Sareen adds - "We are ticketing each panel, then cut parts are separated so panels to print are sent to printing, then someone has to stack them by number so they can go in production. First, we add people to ticket, but tickets, hold the cut for ticketing, then we have people removing the tickets, Sometimes the gum is baked, so now we have people with acetone cleaning it.
Since all other parts are in CAKE STATE except the panels for printing, the sewing time loss is much greater for aligning two panels at every operation, side seams, sleeve set, collar set."
Since all other parts are in CAKE STATE except the panels for printing, the sewing time loss is much greater for aligning two panels at every operation, side seams, sleeve set, collar set."
3. Improved stitching quality:
When you sew t-shirts just after cutting, operators are getting all the components nicely stacked and plies come in sequence as there is no chance of mixing of plies. This help in improving the stitching quality and reducing the process time.
4. Avoid panel missing:
4. Avoid panel missing:
Less chance of missing any garment panels in print workshop. As you are not separating any garment parts for the printing process, there is no way of missing any components in printing process.
5. No edge curling on cut panels:
5. No edge curling on cut panels:
It has been observed that for lightweight cut panels, edge curling happened in the printing process (due to curing and handling). That curling on body sides, reduces the sewing speed for side seam operation as operator need remove the curling before doing side seam overlock. There is a chance of cutting the access side margin causing measurement issue.
This kind of problem will be there when you print on the ready t-shirts. This would improve the productivity of such operations.
6. No extra garment panel printing:
This kind of problem will be there when you print on the ready t-shirts. This would improve the productivity of such operations.
6. No extra garment panel printing:
In the conventional method, you know garment manufacturers cut extra pieces that order quantity, they print all the cutting. You keep a buffer for printing defects/rejections at the printer’s end and you keep buffer in stitching quality rejections. All these incur extra costs in an order processing for extra cutting. In ready garment printing, you can print as many garments as you need to ship. You can reduce printing cost.
Video Link:
Video Link:
You can listen and watch the video here
I would love to hear from you on the challenges and benefits if garment manufacturers move to the new method of printing t-shirts on blank t-shirts.
PS: In my latest publication, Kick Start You T-shirt Business, I have added one chapter on T-shirt printing. You can get more ideas on different methods of t-shirt printing, techniques of t-shirt printing, printing methods, and many other notes.
I would love to hear from you on the challenges and benefits if garment manufacturers move to the new method of printing t-shirts on blank t-shirts.
PS: In my latest publication, Kick Start You T-shirt Business, I have added one chapter on T-shirt printing. You can get more ideas on different methods of t-shirt printing, techniques of t-shirt printing, printing methods, and many other notes.